Sistema SCADA para análisis y control de la producción de bebidas
CASO FEMSA TOLUCA
La planta de Coca Cola FEMSA en Toluca enfrentaba varios problemas urgentes de resolver en el Pozo 4. Las fallas en los armónicos y el variador (incluyendo problemas con la tarjeta de potencia, control de arranques, y generación de ondas reflectivas por la longitud de los cables) causaban interrupciones en la producción.
Además, la planta carecía de una visión clara y unificada de las actividades operativas y de información, lo que dificultaba la optimización del flujo de operación y el uso de equipos.
La necesidad de digitalizar y analizar las principales variables eléctricas de la bomba sumergible y del pozo se hizo evidente para detectar fallas potenciales de forma predictiva y preventiva.
También era esencial programar especificaciones y condiciones recomendadas por el fabricante de la bomba para asegurar su óptimo funcionamiento y cumplir con los requisitos y estándares de la Embotelladora Mexicana de Bebidas.
Para solucionar todos estos problemas, FEMSA acudió a MES Automation, quien desarrolló un sistema SCADA para análisis y control de la producción de bebidas con el fin de simplificar la recopilación, análisis y control de datos de información.
Esta solución estableció y controló el proceso de creación de productos, y facilitó el seguimiento y soporte en el desarrollo de aplicaciones, además de incrementar el uso de la automatización de control tecnológico y proporcionar una mejor metodología para optimizar la eficiencia operativa de la planta.
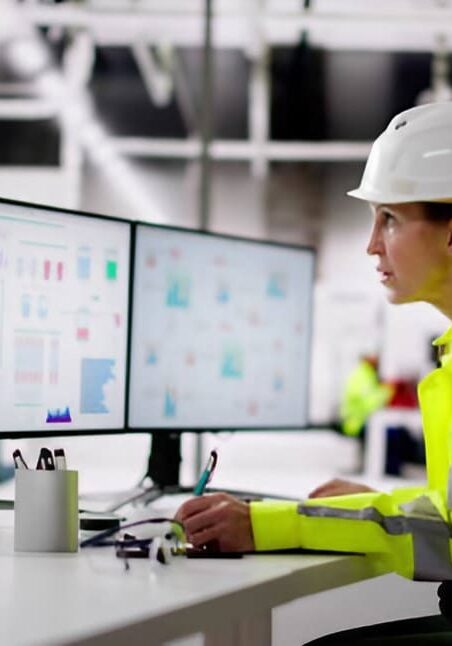
PROBLEMAS Y NECESIDADES
Antes de la implementación de la solución definitiva, por parte de MES Automation, la planta de Coca Cola FEMSA en Toluca enfrentaba múltiples problemas operativos de urgente resolución en su pozo nº 4. Las principales dificultades se centraban en:
- Fallas en los armónicos: Estas fallas interrumpían el funcionamiento adecuado del equipo y afectaban la estabilidad del sistema eléctrico.
- Problemas con el variador: Se presentaban fallas frecuentes en la tarjeta de potencia y el control de arranques, lo que afectaba la eficiencia y confiabilidad del proceso.
- Generación de ondas reflectivas: La longitud de los cables provocaba la generación de ondas reflectivas, que repercutían negativamente en la operación de los equipos.
Estos problemas eran más que suficientes para verse en la urgente necesidad de mejorar la gestión y monitoreo de las operaciones del pozo mediante un sistema SCADA para análisis y control de la producción de bebidas. Para ello, FEMSA identificó varias necesidades esenciales:
- Digitalización y análisis de variables eléctricas: Era fundamental digitalizar y analizar las principales variables eléctricas de la bomba sumergible y del pozo para detectar fallas potenciales de manera predictiva y preventiva.
- Programación de especificaciones recomendadas: Se requería programar las especificaciones y condiciones recomendadas por el fabricante de la bomba para asegurar su óptimo funcionamiento.
- Cumplimiento de requisitos y estándares: La planta debía cumplir con los requisitos y estándares establecidos por la Embotelladora Mexicana de Bebidas para garantizar la calidad y eficiencia de sus operaciones.
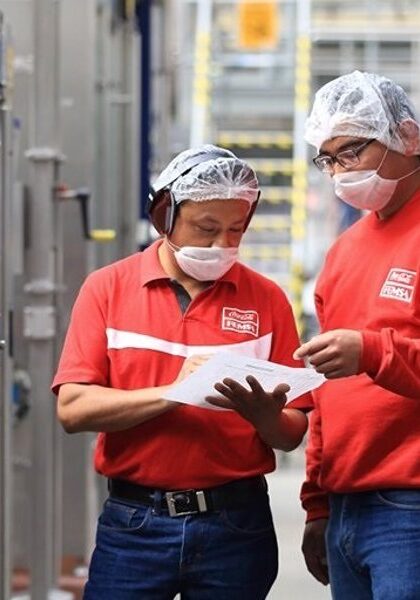
RAZONES
FEMSA decidió solicitar la ayuda de MES Automation para implementar un sistema SCADA para análisis y control de la producción de bebidas debido a varias razones fundamentales que alineaban sus necesidades operativas con las capacidades de MES Automation. Las principales razones incluyen:
Digitalización y análisis de variables críticas
FEMSA necesitaba digitalizar y analizar las principales variables eléctricas de la bomba sumergible y del pozo para la detección de fallas potenciales de manera predictiva y preventiva. MES Automation ofrecía una solución que permitía recopilar, monitorear y analizar estos datos en tiempo real, mejorando así la capacidad de la planta para anticipar y resolver problemas antes de que afectaran la producción.
Programación de especificaciones y condiciones recomendadas
Para asegurar el óptimo funcionamiento de la bomba, era importante seguir las especificaciones y condiciones recomendadas por el fabricante. En este sentido, el sistema SCADA para análisis y control de la producción de bebidas de MES Automation permitía la programación y control de estos parámetros, garantizando que el equipo operara dentro de los límites óptimos establecidos por el fabricante.
Cumplimiento de requisitos y estándares
La planta debía cumplir con los requisitos y estándares establecidos por la Embotelladora Mexicana de Bebidas. El sistema de automatización SCADA para la producción de bebidas no solo cumplía con estos estándares, sino que también mejoraba la eficiencia operativa y la calidad del proceso, asegurando que la planta mantuviera sus altos niveles de desempeño y conformidad.
Visión clara de actividades operativas
Era necesario proveer una visión clara de todas las actividades que se ejecutan en la planta para satisfacer el flujo de operación e información. El sistema SCADA para análisis y control de la producción de bebidas de MES Automation ofrecía herramientas avanzadas para la visualización y gestión de datos, lo que permitía a FEMSA tener un control más preciso y detallado de todas las operaciones en tiempo real.
FEMSA encontró en MES Automation un socio estratégico capaz de ofrecer una solución integral que no solo abordaba los problemas técnicos existentes, sino que también proporcionaba las herramientas necesarias para mejorar la eficiencia, calidad y cumplimiento de sus operaciones.
CAPACIDADES
La implementación del sistema SCADA para análisis y control de la producción de bebidas por parte de MES Automation en la planta de Coca Cola FEMSA, representó un gran avance en la gestión y control de las operaciones del Pozo 4.
Esta solución, además de paliar los problemas técnicos existentes, también introdujo una serie de capacidades avanzadas que mejoraron la eficiencia y la seguridad operativa.
RESULTADOS
El sistema SCADA para análisis y control de la producción de bebidas implantado por MES Automation en la planta de Coca Cola FEMSA ha generado grandes resultados, mejorando la operación del Pozo 4 y proporcionando beneficios claros en varios aspectos importantes.
Estos son los resultados más evidentes obtenidos con esta solución:
Acceso a la aplicación
- Seguridad en el acceso: Solo el personal autorizado tiene acceso a la aplicación, lo que asegura la protección de datos y la integridad de las operaciones.
Pantalla general de la aplicación
- Encabezado: Proporciona una visión general clara y organizada de las funciones principales.
- Visor de alarmas en tiempo real: Permite la visualización inmediata de cualquier problema o anomalía, facilitando una respuesta rápida y eficaz.
Pantalla de operación del Pozo 4
- Pantalla de Ingresar datos: Simplifica el ingreso y actualización de datos operativos.
- Pantalla de configuraciones de control remoto: El sistema de automatización SCADA para la producción de bebidas permite realizar ajustes y configuraciones de forma remota, mejorando la flexibilidad y capacidad de respuesta.
Pantalla de alarmas
- Muestra todas las alarmas activas y el historial de alarmas, lo que facilita el seguimiento y gestión de incidentes.
Pantalla de tendencias
- Proporciona una visualización gráfica de las tendencias en las variables de proceso, ayudando a identificar patrones y anticipar problemas.
Tendencias históricas
- Detalle de herramienta de ajuste gráfica: El sistema SCADA para análisis y control de la producción de bebidas permite el análisis detallado de datos históricos para mejorar la toma de decisiones basadas en tendencias pasadas.
Consultas históricas
- Uso de consultas por el personal de planta: Facilita el acceso a datos históricos para análisis y reportes.
- Ejemplo de consulta para calcular el promedio del valor de flujo: Muestra cómo utilizar las herramientas de consulta para obtener información específica y útil.
- Detalle de herramienta de ajuste de consultas: Permite personalizar las consultas para obtener los datos más relevantes según las necesidades operativas.
Repositorio centralizado de datos de variables de proceso
- Centraliza todos los datos operativos, mejorando la accesibilidad y gestión de la información.
Beneficios de la implementación
Versatilidad en la visualización:
- Sistema visual para la producción y el mantenimiento preventivo.
- Soporte a planes de mejora continua.
- Detección de problemas en líneas de producción, especialmente en equipos esenciales para la generación de agua para la planta.
- Herramienta para mantener el pozo en funcionamiento.
- Estandarización del esquema de visualización de los pozos.
Integración:
- Gestión eficiente de la información recogida de campo.
- Generación de reportes clave para la operación, mantenimiento y gestión de instalaciones.
Surtimiento:
- Capacidad para recoger información de otras fuentes, sensores y pozos.
- Integración de procesos colaterales con el SCADA de agua, permitiendo el control y visualización remota de variables de estado.
Disponibilidad:
- Arquitectura bien definida y segregada físicamente, permitiendo que un pozo opere de forma independiente sin interferencia de otros pozos en desarrollo o mantenimiento.
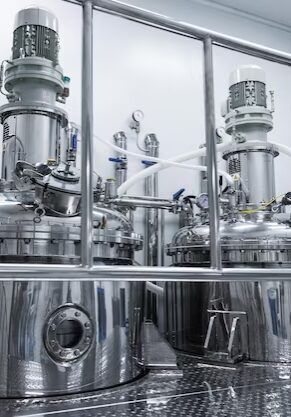
Si hacemos un análisis de estos resultados podemos ver claramente cómo la implementación del sistema SCADA para análisis y control de la producción de bebidas por parte de MES Automation no solo solucionó los problemas iniciales de la planta, sino que también mejoró en gran medida la eficiencia, seguridad y capacidad operativa del Pozo 4, proporcionando una base fuerte para el futuro crecimiento y optimización de las operaciones de Coca Cola FEMSA.
Mejora la eficiencia tu planta con un Sistema SCADA de última generación
Simplifica la recopilación y análisis de datos en tiempo real, mejora la eficiencia operativa y asegura el cumplimiento de los estándares más altos. Detecta fallas potenciales de manera predictiva y preventiva, y mantén un control detallado y seguro de todas tus actividades.
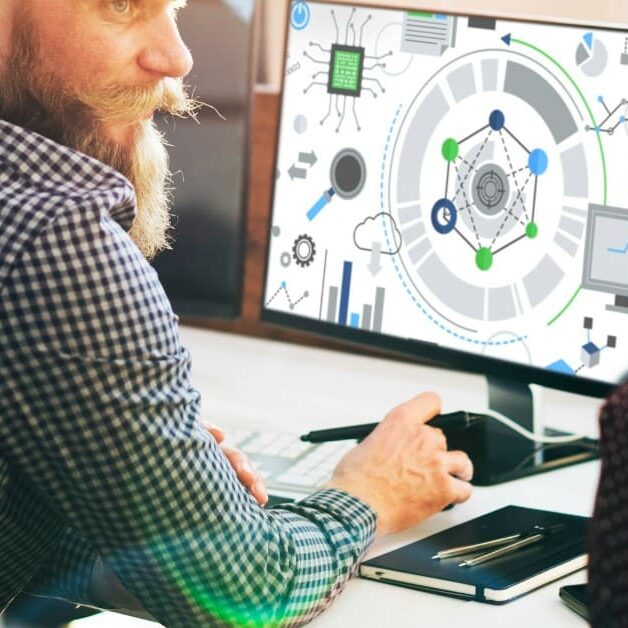