Programación de PLC para la optimización de procesos de limpieza CIP
Caso FEMSA León
En la planta de Coca Cola FEMSA en León, la operación del sistema de limpieza CIP (Clean-in-Place) se gestionaba desde una computadora principal. El operador debía identificar el producto procesado en cada tanque para seleccionar el tipo de limpieza adecuado.
Además, el proceso de limpieza seguía una serie de pasos predefinidos, realizados en una secuencia programada con tiempos específicos para cada etapa.
Antes de iniciar la secuencia de limpieza, era importante asegurarse de que parámetros como la temperatura y los niveles de agua estuvieran dentro de los rangos permitidos.
El proceso de limpieza comenzaba con la selección del tipo de limpieza a realizar. Luego, se seleccionaba el tanque a limpiar. Finalmente, se ejecutaba la secuencia de limpieza, donde cada paso tenía un tiempo de ejecución preestablecido.
Aunque las secuencias de limpieza estaban programadas para recircular y almacenar el agua cuando la concentración de contaminantes estaba dentro de los parámetros aceptables, no existía un indicador en tiempo real para confirmar esta condición.
Esto suponía un grave inconveniente para la eficiencia en el uso del agua y la fiabilidad del proceso de limpieza. Por ello, FEMSA recurrió a MES Automation para encontrar la solución óptima a sus problemas, mediante la programación de PLC para la optimización de procesos de limpieza CIP.
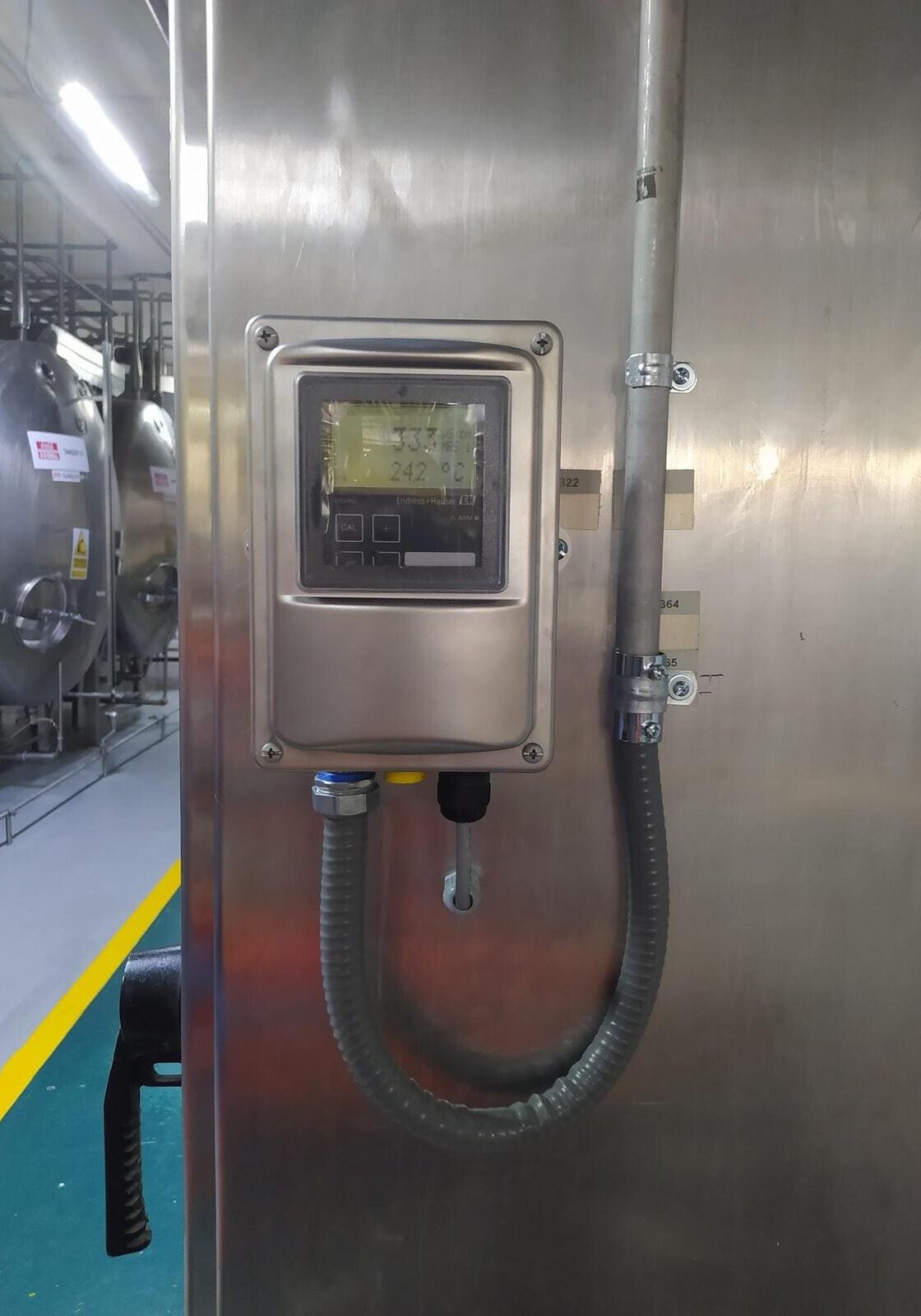
PROBLEMAS Y NECESIDADES
La eficiencia del sistema de limpieza CIP (Clean-in-Place) es esencial para mantener la producción en óptimas condiciones en la planta de Coca Cola FEMSA. Como ya mencionamos, este sistema se gestiona desde una computadora principal, donde el operador selecciona el tipo de limpieza adecuado para cada tanque, siguiendo una secuencia predefinida con tiempos específicos.
Sin embargo, se identificaron varios problemas urgentes que afectaban la eficiencia y la confiabilidad del proceso. Desde la obsolescencia de los controladores y el software hasta la falta de indicadores en tiempo real para verificar la concentración de contaminantes, estos inconvenientes ponían en relieve la necesidad de actualizar y mejorar el sistema para optimizar la recuperación de agua y modernizar el control del proceso mediante la automatización de PLC para limpieza CIP.
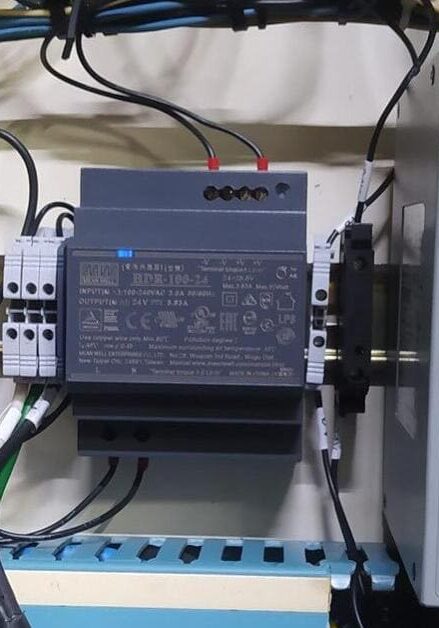
RAZONES
MES Automation cuenta con amplia experiencia en la implementación de sistemas de automatización y control industrial. Su avanzado conocimiento técnico en programación de PLC para la optimización de procesos de limpieza CIP, actualización de controladores PLC y en la integración de tecnologías modernas, les posicionó como el socio ideal para hacer frente a los problemas de obsolescencia en los equipos y software de FEMSA.
Además, MES Automation se erigió como el socio ideal al contar con otras fuertes capacidades como:
Soluciones personalizadas
La automatización de PLC para limpieza CIP de MES Automation podía adaptarse a las necesidades específicas de la planta de FEMSA. Esto incluía la capacidad de diseñar e implementar una secuencia de recuperación de agua dentro del sistema CIP, esencial para mejorar la eficiencia del uso del agua y reducir costos operativos.
Innovación y actualización tecnológica
La empresa tenía acceso a las últimas tecnologías y herramientas de software, como FactoryTalk RSView 32 y sensores avanzados de conductividad. Su experiencia en innovación aseguraba que las soluciones propuestas no solo resolverían los problemas actuales, sino que también prepararían el sistema para futuras necesidades y expansiones.
Optimización de recursos hídricos
Una de las principales razones fue la capacidad de MES Automation para implementar la recuperación de los últimos enjuagues del CIP con ozono, permitiendo que el agua recuperada se utilizara en otros procesos. Esta capacidad era esencial para FEMSA, ya que ayudaba a maximizar el aprovechamiento del agua y a cumplir con los objetivos de sostenibilidad.
Soporte y mantenimiento
Además de la experiencia en programación de PLC para la optimización de procesos de limpieza CIP, MES Automation ofrecía un robusto servicio de soporte y mantenimiento, lo cual era un elemento muy importante para garantizar la continuidad operativa y la longevidad del sistema actualizado. Su capacidad para proporcionar actualizaciones y soporte técnico continuo era un factor decisivo para FEMSA.
Éxitos previos y reputación
La reputación de MES Automation en el sector de la automatización y sus casos de éxito previos en proyectos similares proporcionaron a FEMSA la confianza necesaria para proceder con esta colaboración. Los testimonios positivos y los resultados demostrados en otras plantas industriales reforzaron la decisión de elegirlos.
CAPACIDADES
Para hacer frente a los problemas identificados en el sistema de limpieza CIP de la planta de Coca Cola FEMSA, se requerían capacidades específicas que permitieran implementar mejoras efectivas y sostenibles.
MES Automation fue seleccionado por su habilidad para proporcionar soluciones tecnológicas avanzadas y personalizadas de programación de PLC para la optimización de procesos de limpieza CIP, capaces de mejorar los procesos de limpieza y recuperación de agua.
Veamos las capacidades clave que MES Automation implementó para resolver los problemas técnicos y operativos del sistema CIP, asegurando una operación más eficiente y confiable.
RESULTADOS
La programación de PLC para la optimización de procesos de limpieza CIP que realizó MES Automation en la planta de Coca Cola FEMSA produjo magníficos resultados que mejoraron la eficiencia y sostenibilidad del sistema de limpieza CIP. Esta transformación no solo optimizó el proceso de limpieza, sino que también tuvo un impacto positivo en el aprovechamiento de los recursos hídricos y en la modernización de los sistemas de control.
Instalación de sensor de conductividad
Se instaló un sensor de conductividad en la tubería de retorno del CIP en la sala de jarabes, permitiendo la medición precisa de los niveles de contaminantes en el agua.
Mejora en el monitoreo en tiempo real
El sensor de conductividad se conectó a un indicador en el tablero de control, lo que permitió a los operadores visualizar las mediciones en tiempo real. Esto mejoró significativamente la capacidad de monitoreo y control del proceso de limpieza.
Recuperación de agua
La programación de PLC para la optimización de procesos de limpieza CIP sirvió para implementar un sistema para recuperar el agua desde el segundo enjuague del CIP, utilizando mediciones de conductividad para asegurar que los niveles de contaminantes estuvieran por debajo de los límites permitidos.
Esto dio lugar a una mayor cantidad de agua reutilizable en otros procesos, mejorando la eficiencia del uso de recursos hídricos.
Actualización y programación del PLC
La programación del PLC fue actualizada para incluir la nueva secuencia de recuperación de agua. Esto incluyó la conexión del medidor de conductividad a una entrada analógica del PLC y la programación de la secuencia de limpieza con ozono para recuperar el agua de manera eficiente.
Visualización y reportes mejorados
Los cambios en la programación del PLC se reflejaron en la interfaz HMI FactoryTalk RSView 32, lo que permitió visualizar y reportar los valores de conductividad y la cantidad total de agua recuperada. Esto proporcionó datos valiosos para la gestión del proceso y facilitó la toma de decisiones más inteligentes.
Publicado originalmente el 1 agosto 2024, actualizado el 7 octubre 2024