Sistema ANDON para manufactura de productos eléctricos y energía
Caso Generac Pachuca
GENERAC, con más de 60 años de experiencia en el mercado latinoamericano y especializada en productos y soluciones de energía para los sectores residencial, comercial e industrial, se encontraba en una situación de riesgo donde la optimización de sus procesos productivos era un asunto a resolver de manera inminente.
En su planta de producción en Villa de Tesontepec, Puebla, enfrentaba varios problemas que afectaban a la eficiencia y la productividad de la empresa.
Carecían de un sistema de indicadores de alerta que permitiera a los operadores identificar y reportar rápidamente situaciones anormales en las máquinas o paros de producción. Esta falta de indicadores dificultaba la capacidad de solicitar ayuda de manera eficiente, lo que resultaba en tiempos prolongados de inactividad.
Además, no había un proceso formalizado para registrar y gestionar los tiempos de paro en las líneas de producción, lo que impedía la recopilación de datos cruciales para analizar y mejorar los tiempos de respuesta y solucionar problemas operativos.
La ausencia de un sistema estándar para gestionar y escalar problemas operativos también impedía una comunicación fluida entre los operadores y el departamento de soporte, afectando negativamente la productividad.
Con el objetivo de mejorar su rentabilidad y optimizar sus procesos de producción, GENERAC decidió implementar un sistema ANDON para manufactura de productos eléctricos y energía en sus instalaciones, buscando una solución tecnológica que monitoreara en tiempo real los paros de producción y permitiera una gestión eficiente de los eventos, reduciendo así los tiempos de inactividad y mejorando la eficiencia general de la planta.
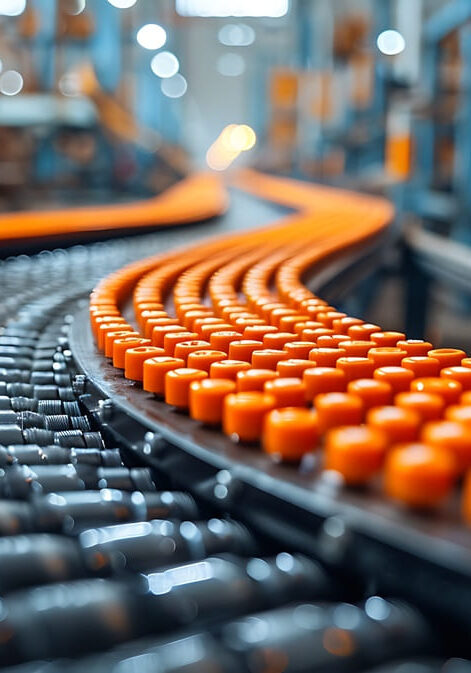
PROBLEMAS Y NECESIDADES
Generac se enfrentaba a una serie de retos importantes en su planta de producción que incidían directamente en la eficiencia operativa y la productividad. A pesar de su larga experiencia en el mercado de generación de energía de respaldo, la falta de herramientas tecnológicas adecuadas se traducía en problemas frecuentes en la gestión de sus procesos productivos.
Reconociendo la necesidad de mejorar estos aspectos, Generac identificó una serie de necesidades principales para mejorar sus operaciones y asegurar una mayor rentabilidad.
Problemas
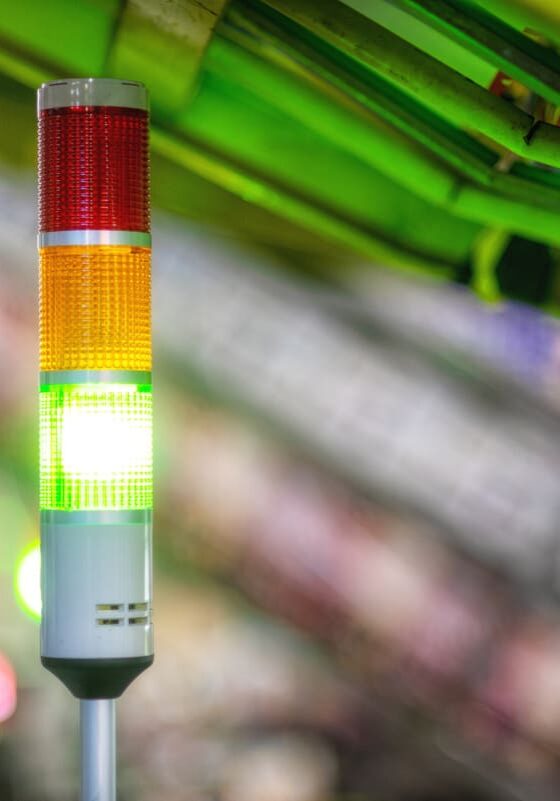
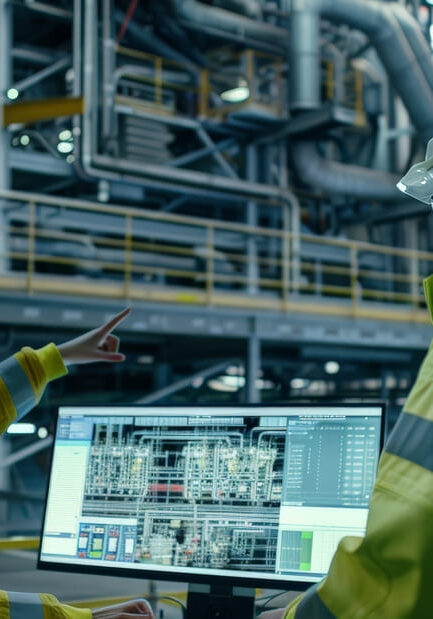
Necesidades
RAZONES
Generac decidió implementar el sistema ANDON para manufactura de productos eléctricos y energía de MES Automation debido a una serie de factores esenciales que estaban directamente alineados con sus objetivos de mejorar la eficiencia operativa y la rentabilidad en su planta de producción.
Optimización de la productividad
La falta de un sistema eficiente para monitorear y gestionar los tiempos de paro en las líneas de producción afectaba en gran medida a la productividad de Generac. Implementar el sistema ANDON para productos eléctricos y energéticos permitió a la empresa tener un control en tiempo real sobre los eventos de paro, facilitando una respuesta rápida y efectiva ante cualquier incidencia.
Esto dio lugar a una reducción considerable de los tiempos de inactividad y un aumento del rendimiento operativo.
Mejora en la gestión de incidencias
Antes de la implementación del sistema ANDON para manufactura de productos eléctricos y energía de MES Automation, los operadores no contaban con una herramienta para solicitar ayuda de manera eficiente, lo que retrasaba la resolución de problemas.
Con el sistema ANDON de señalización visual para manufactura eléctrica, Generac pudo estandarizar los procedimientos para gestionar los llamados de ayuda, asegurando que cada incidencia fuera atendida de manera oportuna y siguiendo un proceso definido.
Esto mejoró notablemente la gestión de incidencias y la coordinación entre los operadores y el departamento de soporte.
Escalado automático de alertas
La capacidad del sistema ANDON para escalar alertas de manera automática fue una característica esencial para Generac. Esta funcionalidad garantizó que los problemas no resueltos en un tiempo determinado fueran rápidamente notificados a niveles superiores o a otros departamentos de soporte, acelerando la solución de problemas urgentes y minimizando el impacto en la producción.
Adaptabilidad y flexibilidad del sistema
MES Automation ofrecía un sistema adaptable y flexible, capaz de configurarse según las necesidades cambiantes de la fábrica. Esto permitió a Generac ajustar de forma dinámica los flujos y estados de los eventos, asegurando que el sistema siempre estuviera alineado con las exigencias operativas de la planta. La facilidad de configuración y la capacidad de adaptación fueron aspectos fundamentales para elegir esta solución.
Documentación y análisis en tiempo real
Generac necesitaba una solución que permitiera documentar en tiempo real las incidencias y las acciones tomadas para resolverlas. El sistema ANDON para manufactura de productos eléctricos y energía de MES Automation proporcionó una plataforma para registrar todos los eventos y sus respectivas soluciones, generando una base de datos valiosa para el análisis posterior.
Monitoreo visual del estado de producción
La posibilidad de mostrar el estado de cada estación de trabajo en tiempo real mediante pantallas ubicadas en el área de producción ayudó a mantener a todos los operadores y supervisores informados sobre el funcionamiento de las máquinas. Esto no solo mejoró la comunicación y la coordinación en la planta, sino que también permitió una rápida identificación y respuesta ante cualquier anomalía.
CAPACIDADES
La implementación del sistema ANDON para manufactura de productos eléctricos para Generac en la Planta Villa de Tesontepec, requirió una serie de capacidades esenciales para asegurar que el sistema cumpliera con los objetivos planteados de optimización y mejora de los procesos productivos.
Estas son las capacidades más destacadas del sistema ANDON que contribuyeron a resolver los problemas identificados para satisfacer las necesidades de la planta.
La implementación del sistema ANDON en Generac México dotó a la planta de una serie de capacidades avanzadas que fueron esenciales para mejorar la gestión de los procesos productivos. Desde el monitoreo en tiempo real y las indicaciones visuales de estado, hasta el escalado de alertas y la generación de reportes detallados, cada una de estas capacidades contribuyó a optimizar la productividad, reducir los tiempos de inactividad y mejorar la eficiencia operativa en general.
RESULTADOS
La implementación del sistema ANDON para manufactura de productos eléctricos y energía de MES Automation en la planta de Generac dio lugar a grandes resultados, mejorando considerablemente la productividad y la eficiencia operativa. Estos son los beneficios y mejoras logradas tras la implementación del sistema:
Aumento de la productividad
Uno de los resultados más notables fue el incremento del 15% en la productividad de la fábrica. Esto se logró gracias a una gestión más eficiente de las ayudas de paro y la minimización de los tiempos de inactividad. La capacidad de identificar y resolver rápidamente las incidencias permitió estar más centrados en la producción y mejorar el rendimiento general.
Reducción de tiempos de paro
La implementación del sistema de monitoreo de paros en la fabricación de productos eléctricos y energéticos permitió reducir entre un 12% y 16% los tiempos de paro, únicamente al mejorar los tiempos de respuesta ante los eventos.
El escalado automático de alertas y la documentación precisa de cada evento contribuyeron a solucionar los problemas de manera más ágil, disminuyendo considerablemente los tiempos de inactividad.
Mejora en la gestión de problemas
El sistema sistema ANDON para manufactura de productos eléctricos y energía de MES Automation permitió documentar en tiempo real los problemas que afectaban a la producción, facilitando la identificación y el análisis de las causas más comunes de fallas.
Esto permitió a Generac enfocar sus actividades de mantenimiento en las áreas más importantes, generando planes de acción efectivos para prevenir futuras incidencias y mejorar continuamente los procesos.
Registro y análisis de eventos
La capacidad de registrar eventos inesperados en tiempo real y proporcionar soluciones rápidas y prácticas fue esencial para la operación de la planta. Los operadores podían notificar a los supervisores sobre fallas y otros contratiempos de manera inmediata, permitiendo una toma de decisiones precisas.
Además, la generación de una base de datos detallada ayudó a planificar mantenimientos futuros y a medir el impacto de las tareas realizadas por el equipo de mantenimiento.
Optimización de procesos y reducción de costes
El sistema ANDON de señalización visual para manufactura eléctrica de MES Automation ayudó a eliminar operaciones que no agregaban valor a los procesos y a identificar fallas operativas, asegurando que siempre hubiera suficiente material para la línea de producción.
Esto no solo optimizó los procesos, sino que también redujo los costes operativos al eliminar ineficiencias y mejorar la utilización de los recursos disponibles.
Incremento de los niveles de información
La implementación del sistema ANDON para el control de paros en la producción eléctrica y de energía incrementó en gran medida los niveles de información disponibles para operadores, supervisores y directores.
La recopilación de datos y la generación de reportes, incluyendo gráficas de tendencias, proporcionaron una visión clara y detallada del estado de las máquinas y la producción. Esto facilitó una mejor planificación y una mejor toma de decisiones a todos los niveles de la empresa.
Respuesta eficiente ante contingencias
Cuando el tiempo de solución de un evento excedía el estándar configurado, el sistema enviaba notificaciones a los niveles medios y superiores de la planta, asegurando una rápida respuesta ante incidencias.
Este escalado de eventos a los departamentos de soporte garantizó que todos los problemas urgentes fueran atendidos de manera eficiente y eficaz.
Herramientas de notificación
El sistema ANDON para manufactura de productos eléctricos y energía de MES Automation configuró notificaciones a través de tres herramientas principales: correo electrónico, alertas visuales en televisores y notificaciones en relojes.
Esta diversidad de canales de notificación aseguró que todos los involucrados estuvieran informados en tiempo real sobre el estado de los eventos y pudieran tomar las acciones necesarias de inmediato.
Documentación y seguimiento de eventos
El sistema permitió el registro del nombre de usuario que atendía un evento de paro mediante autenticación, reconocimiento de eventos generados por la activación de botones digitales, y medición automática de tiempos de atención y solución.
Además, facilitó la clasificación de eventos y asignación de razones de falla con comentarios, mejorando la documentación y el análisis de la información.
SOLUCIONES AVANZADAS DE AUTOMATIZACIÓN
Los resultados obtenidos tras la implementación del sistema de señalización visual para manufactura eléctrica de MES Automation en Generac México fueron múltiples y altamente beneficiosos. La gestión eficiente de ayudas de paro, la reducción de tiempos de inactividad, la optimización de procesos y la mejora en la toma de decisiones contribuyeron significativamente a mejorar la productividad y la eficiencia operativa de la planta.
La capacidad de documentar y analizar eventos en tiempo real, junto con la escalación automática de alertas, aseguraron que Generac pudiera mantener un alto nivel de rendimiento y continuar mejorando sus operaciones de manera continua.
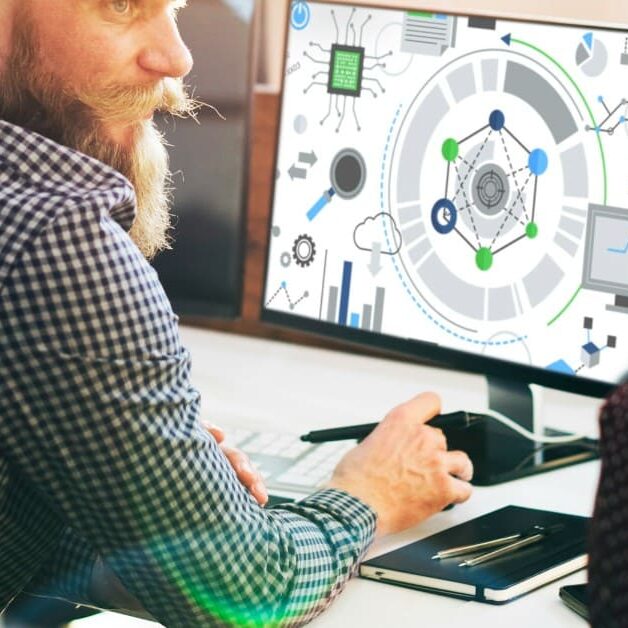
Publicado originalmente el 21 agosto 2024, actualizado el 7 octubre 2024