La conectividad a múltiples dispositivos, el manejo situacional de alarmas y la automatización integrada, entre otras potencialidades, hacen de los sistemas SCADA una valiosa solución para la supervisión de procesos de manufactura.
El experimentado ingeniero industrial Giovanni Palermo, socio-director de una empresa especializada en aplicaciones y soluciones de lean manufacturing, destaca que estos sistemas son capaces de identificar y reducir múltiples riesgos de la línea de producción, entre ellos:
- Pérdidas en la producción por desviaciones en el cumplimiento de especificaciones
- Pérdidas financieras
- Desastres ambientales/caos de funcionamiento
- En el peor de los casos, pérdida de vidas humanas por accidentes.
- Costos extra asociados a la no calidad
Tomando como referencia impresiones y valoraciones de este especialista, en las próximas líneas explicaremos cuáles potencialidades y funciones le permiten al sistema SCADA prevenir riesgos y qué otras ventajas aporta a las fábricas.
¡Lee hasta el final!
¿Cómo un sistema SCADA reduce los riesgos en la línea de producción?
De acuerdo a Palermo, quien tiene 23 años de experiencia en el giro industrial, el elemento central de un sistema SCADA en cuanto a disminución de riesgos es el aporte de conciencia situacional (del inglés situational awareness) al operador.
Este concepto, también conocido como conciencia operacional, hace referencia a la percepción y conocimiento del operador con respecto al ambiente dinámico de proceso y las amenazas potenciales, así como a la capacidad del mismo para realizar proyecciones o pronosticar qué ocurrirá.
Para que esto sea posible, el sistema SCADA debe contener interfaces gráficas con despliegue situacional de alarmas, que permiten alertar e informan sobre el comportamiento de las variables críticas de la línea de producción y aspectos como la seguridad.
Estas señales y avisos son el resultado final de un proceso automatizado de adquisición de datos, impulsados por el sistema gracias a plataformas de software (generalmente alojadas en servidores) que pueden interactuar con una amplia gama de dispositivos de control de procesos industriales, tales como bombas, motores, sensores y válvulas.
Incluso, los mejores sistemas SCADA incluyen protocolos de comunicación industrial como OPC, Suite Link, DDE, Profinet y Profibus, capaces de conectar con dispositivos utilizando medios físicos como redes de control local y seriales directos.
Este práctico acceso a la información clave, en tiempo real, permite mantener un riguroso control sobre el proceso y disponer de los datos necesarios en forma de reportes para tomar las mejores decisiones.
Otros grandes beneficios de un sistema SCADA
Son muchas las formas en que un sistema SCADA puede ayudar a tu fábrica, más allá de la reducción de riesgos y la prevención de eventos no deseados.
Para Giovanni Palermo, otra de las potencialidades de estas soluciones que merece ser destacada es la capacidad para optimizar el tiempo y las horas-hombre.
“Los recursos y el tiempo son mejor aprovechados gracias a la digitalización de reportes y de otras tareas que dejan de hacerse localmente, como el registro de la temperatura cada 3 horas, por ejemplo”.
El experto destaca que la reducción de carga laboral y la flexibilización de la dinámica de trabajo ayuda a que el operador realmente pueda centrarse en agregar valor a los procesos.
“En vez de llenar una planilla, el operador puede enfocarse en labores de supervisión y análisis de los procesos, identificando aspectos que aporten valor y mejores resultados”.
Además de proporcionar control en tiempo real, otra condición a resaltar del sistema SCADA es el almacenamiento centralizado de data histórica.
Esto permite evaluar la dinámica de producción en determinados periodos y medir la evolución y los resultados. También, el análisis de datos históricos es clave para identificar puntos de mejora o patrones de comportamientos no deseados.
Lo dicho hasta ahora permite concluir que un sistema SCADA puede jugar un papel fundamental en la reducción del costo total de operación de una planta, gracias al aporte de información histórica y en tiempo real y al desarrollo de la conciencia situacional para proyectar escenarios y atender a tiempo problemas que puedan generar gastos extra.
Caso de éxito
Palermo destaca que los sistemas SCADA se adaptan a las necesidades y requerimientos de diferentes industrias, entre ellas la química, la de potabilización de aguas y la alimentaria.
En el caso del giro de alimentos y bebidas, estas soluciones son especialmente útiles para mantener un riguroso control de las etapas de procesamiento, como lo demuestra el caso de éxito de Jugos del Valle.
A través de la implementación de un sistema SCADA, Jugos del Valle logro visualizar y controlar a traves de interfases graficas muy intuitivas HMI (Human Machine Interface), 23 homogenizadores y pasteurizadores de su planta del Tepotzotlán, en el estado de México.
En concreto, Juegos del Valle integró el cuarto de control provisto por el sistema al anillo de redes de sus servidores, desplegando un monitoreo preciso de las principales variables de la línea de procesamiento. Esto le proporcionó beneficios como:
- Visualización gráfica de las funciones principales para todos los pasteurizadores.
- Integración de toda la información de los pasteurizadores en una plataforma común de automatización, que permite una eficaz seguimiento de las variables de procesos criticos desde una sala de control.
- Seguimiento, en tiempo real, del comportamiento de las principales variables del proceso.
- Visualización y Gestion de Alarmas del proceso, en tiempo real.
¡Y listo! Si leíste hasta aquí ya sabes cómo un sistema SCADA reduce riesgos y cuáles son las principales potencialidades de esta solución.
Además de lo mencionado, es importante resaltar que estas aplicaciones pueden ser tolerantes a fallas, por lo cual garantizan un funcionamiento normal aunque se produzcan errores de hardware o software.
Esto es posible gracias a una doble configuración, que consta de un sistema primario y otro de respaldo. En otras palabras, la solución ejecuta servicios primarios y, automáticamente, sincroniza los mismos en un modo “en espera”.
De esa manera, en caso de que se identifique una falla en los servicios activos, se ejecutarán los que están en estatus de espera, sin que se deban realizar configuraciones manuales ni experimentar eventos de paro.
¿Te pareció interesante este material? Si tienes alguna duda o necesitas más información sobre la implementación de un sistema SCADA, ¡no dudes en escribirnos en la casilla de comentarios! ¡Te atenderemos con gusto!
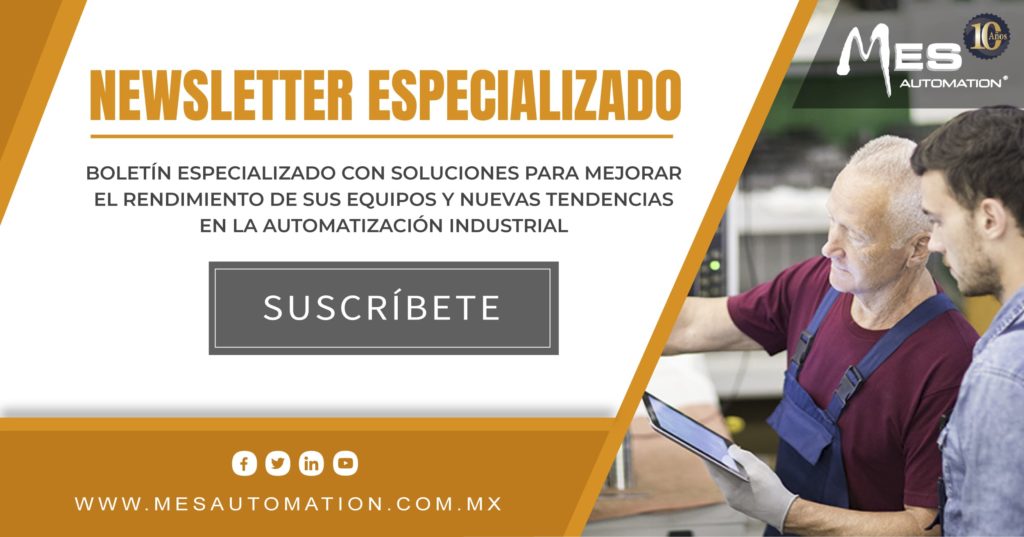
Publicado originalmente el 22 mayo 2020, actualizado el 3 enero 2022