Un sistema ANDON, es una solución utilizada para mostrar el estado de la producción, a través de señales de audio y señales luminosas indican las condiciones de trabajo en el piso de producción. Si buscas implementar un sistema de ayuda a la producción para disminuir los tiempos de paros imprevistos, el sistema ANDON es una opción que debes tomar en cuenta.
El sistema ANDON de Mes Automation es una plataforma visual de información para la producción esbelta que se caracteriza por brindar grandes beneficios, a continuación daremos a conocer 5 de ellos.
Registro de eventos inesperados
El registro en tiempo real de eventos inesperados es crucial para asegurar la continuidad de los procesos en una planta de producción. Con un sistema ANDON, los operadores pueden identificar fallas en máquinas, interrupciones de la línea o cualquier contratiempo que afecte la producción de manera inmediata.
Esto permite no solo una rápida detección, sino también la posibilidad de reaccionar de manera proactiva, evitando que un problema menor se convierta en una parada significativa de la producción.
Los operadores, al ser notificados instantáneamente, pueden activar protocolos de emergencia, solicitar soporte técnico o tomar decisiones correctivas en el acto, minimizando así las interrupciones y los tiempos muertos.
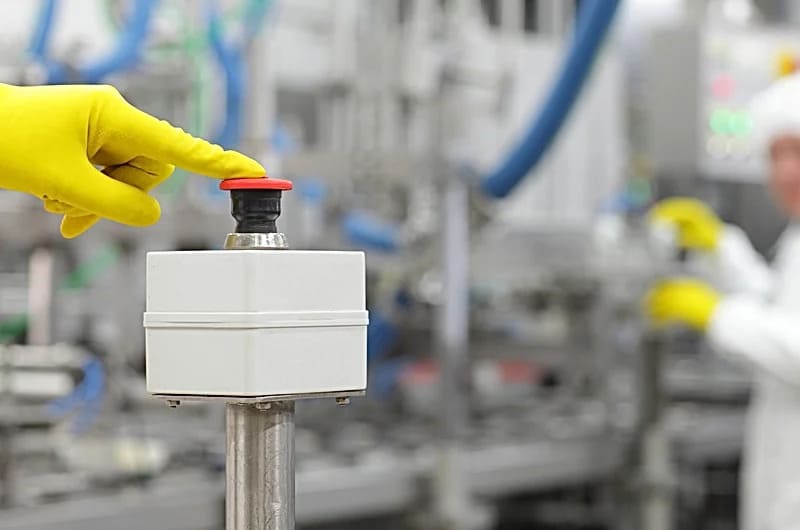
Rápida repuesta
El sistema ANDON no solo se encarga de registrar los eventos, sino que facilita una respuesta rápida y eficaz. Tras notificar al supervisor sobre una falla, el sistema permite clasificar el tipo de problema, priorizar su urgencia y asignarlo al equipo adecuado para su resolución. Esta capacidad de categorizar y escalar rápidamente los problemas reduce significativamente los tiempos de respuesta, lo que resulta en una mayor eficiencia operativa.
La herramienta, además, documenta cada incidente, lo que permite un análisis posterior que ayuda a prevenir fallas futuras y mejorar continuamente los procedimientos de resolución de problemas.
Un ejemplo práctico de esta rápida respuesta se puede observar en una planta automotriz donde un operador detecta una avería en una de las máquinas de soldadura robótica de la línea de montaje. Al activarse el sistema ANDON, se envía de inmediato una alerta al supervisor y al equipo de mantenimiento. El sistema categoriza el problema como una falla crítica en la soldadura, dado que impacta directamente en la integridad estructural de los vehículos.
El equipo de mantenimiento recibe la notificación con una prioridad alta y es dirigido rápidamente a la ubicación específica de la máquina defectuosa. Mientras tanto, el sistema ANDON también notifica a los responsables de calidad para evaluar si las piezas afectadas deben retirarse de la línea. Gracias a la rápida escalación del problema, el equipo de mantenimiento repara la máquina en cuestión de minutos, evitando paradas prolongadas y reduciendo el impacto en la producción.
Al final, el incidente queda documentado con detalles sobre la naturaleza de la falla, el tiempo de respuesta y las acciones tomadas, lo que permite realizar un análisis posterior y ajustar el plan de mantenimiento preventivo, reduciendo la probabilidad de que se repita la misma avería en el futuro.
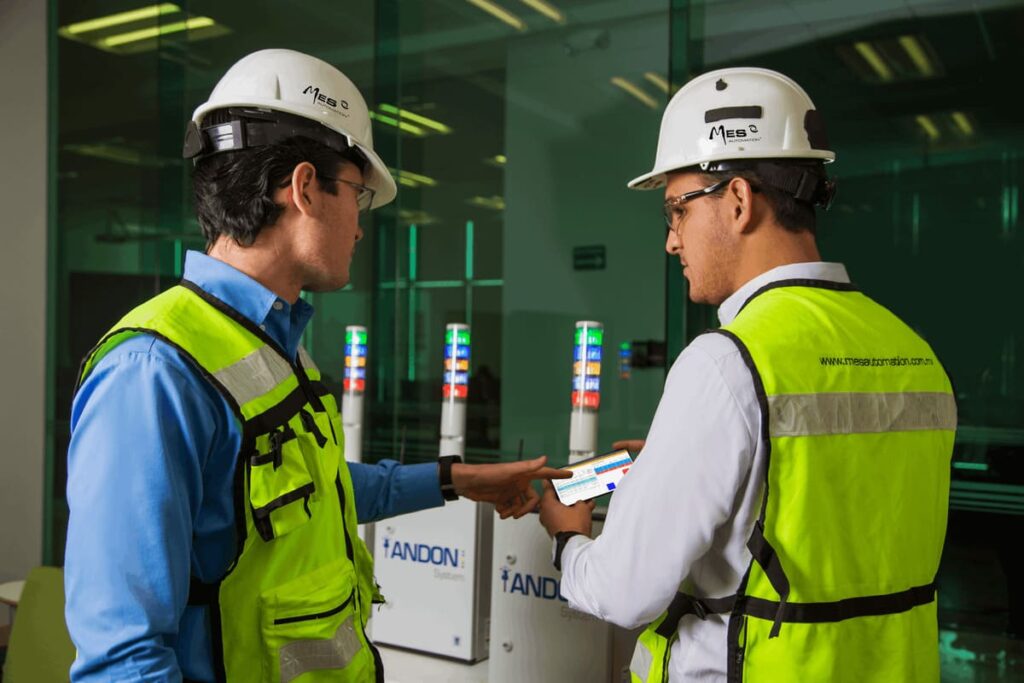
Reducción de costes y optimización del tiempo
Un sistema ANDON permite identificar y eliminar aquellas operaciones o tareas que no aportan valor directo al proceso de producción, ayudando a optimizar el flujo de trabajo. Esto contribuye a una mejor gestión del inventario, garantizando que la cantidad adecuada de materiales esté disponible cuando se necesite, y a la detección temprana de problemas operativos que podrían causar ineficiencias o desperdicio de recursos.
La optimización de los procesos, al reducir tiempos improductivos y prevenir problemas antes de que escalen, genera una reducción en los costes operativos, incrementando la rentabilidad de la planta sin comprometer la calidad de los productos.
Incremento de los niveles de información
Implementar un sistema ANDON no solo mejora la capacidad de respuesta ante fallas, sino que también proporciona una visión completa del rendimiento de la planta. Operadores, supervisores y directores tienen acceso a información clave en tiempo real sobre el estado de las operaciones, permitiendo una toma de decisiones más informada y precisa. Además, el sistema recopila datos históricos, que pueden ser utilizados para generar reportes detallados y gráficas de tendencias, lo cual es invaluable para realizar análisis de mejora continua.
Esto habilita a las empresas a identificar áreas de oportunidad, establecer patrones de comportamiento en las fallas y tomar medidas proactivas que mejoran la eficiencia y productividad a largo plazo.
Supongamos que en la línea de montaje de una planta automotriz, un operador detecta que una pieza defectuosa (como un componente del sistema de frenado) ha sido instalada incorrectamente o no cumple con los estándares de calidad establecidos.
- Notificación inmediata y detención de la línea: Al notar el problema, el operador activa el sistema ANDON, lo que envía una alerta en tiempo real al supervisor y a los departamentos de calidad y mantenimiento. Simultáneamente, el sistema puede detener automáticamente la línea de ensamblaje para evitar que más vehículos avancen con el defecto.
- Clasificación y respuesta rápida: El sistema permite que el operador clasifique el tipo de problema (en este caso, un defecto en la instalación del componente de freno) y lo escale según su gravedad. Los supervisores reciben la notificación, evalúan la situación y asignan al equipo de mantenimiento o calidad para corregir el error.
- Documentación y análisis: Mientras se corrige el problema, el sistema ANDON recopila datos sobre el evento, como el tiempo de respuesta, el equipo involucrado y la causa raíz del defecto. Esta información se documenta automáticamente y queda disponible para su posterior análisis.
- Optimización y mejora continua: Con los datos recopilados, la planta puede analizar la recurrencia de este tipo de fallas en el sistema de frenado y determinar si se deben hacer ajustes en el proceso de ensamblaje, en el suministro de piezas o en la capacitación del personal. Los reportes generados, que incluyen gráficas de tendencias y estadísticas de eventos similares, permiten a la planta automotriz identificar áreas de mejora y aplicar cambios que optimicen la producción, minimizando defectos y reduciendo los tiempos de parada en el futuro.
Este enfoque asegura que los problemas se resuelvan rápidamente y que el impacto en la producción sea mínimo, mejorando la eficiencia general de la planta y asegurando la calidad del producto final.
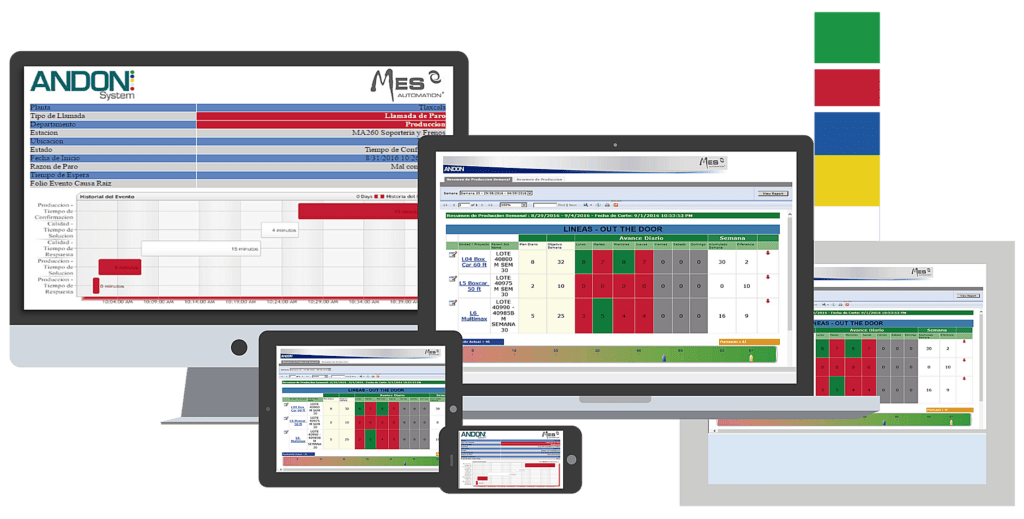
Respuesta ante contingencias
Cuando un incidente no se resuelve en un tiempo estipulado, el sistema ANDON escala automáticamente la alerta a los niveles superiores de la organización, asegurando que la atención al problema sea inmediata y adecuada.
Este tipo de escalación no solo asegura que la falla sea tratada por el personal idóneo, sino que también involucra a los departamentos de soporte técnico o de mantenimiento cuando sea necesario. Esta funcionalidad es vital para gestionar contingencias graves que podrían impactar la producción de manera significativa, garantizando que la planta pueda mantener un flujo de trabajo constante y minimizar las paradas prolongadas.
El sistema actúa como un garante de la eficiencia operativa, proporcionando una estructura clara de escalación y comunicación para resolver problemas complejos de manera ágil.
Ya que estás interesado en conocer más beneficios acerca de un sistema ANDON para procesos productivos, te invitamos a contactar a un asesor de MES Automation, quien te guiará en el proceso de digitalización de la producción de tu empresa.
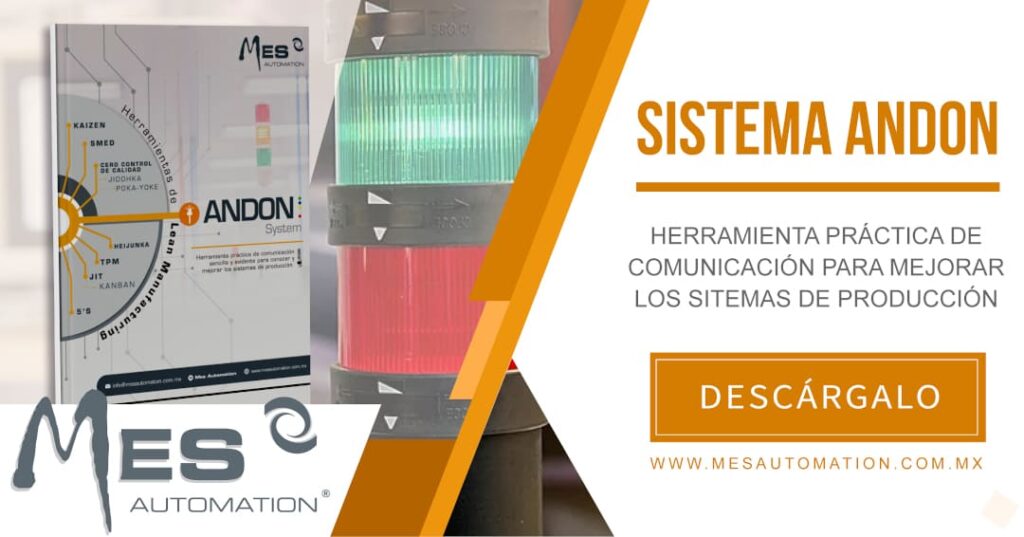
Publicado originalmente el 19 junio 2019, actualizado el 11 octubre 2024